Our stakes
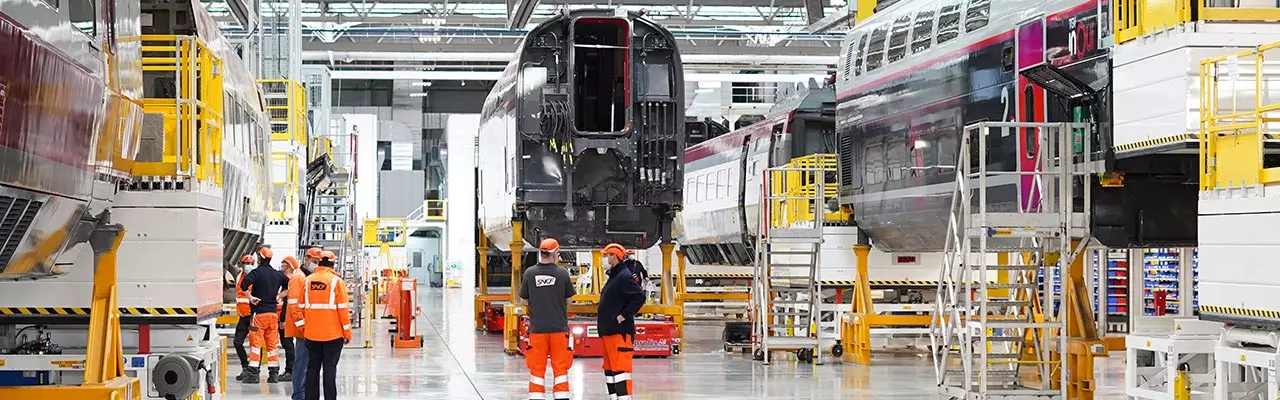
Keeping pace with innovation
Every day, in our workshops and design offices, our teams innovate and experiment, with the aim of industrializing new ideas! Today is already tomorrow!
4 innovative maintenance solutions
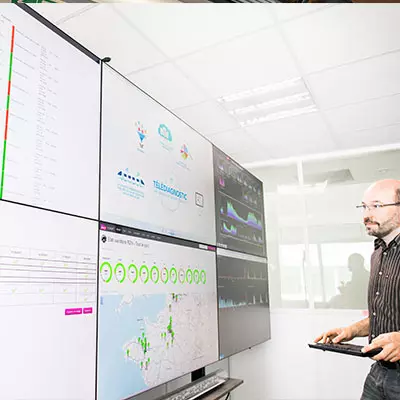
1. Predictive maintenance
Predictive maintenance means not taking preventive action for nothing. Instead, we intervene at just the right moment, just before a breakdown occurs. This is achieved by continuously analyzing the data and behavior of equipment (notably doors, air conditioning, brakes, batteries, compressors, pantographs, safety equipment, etc.), supplemented by other operating information (position, number of passengers, presence of ice, etc.).
4 functions are available for remote diagnosis and predictive maintenance:
- Know the state of the train in real time.
- Anticipate breakdowns.
- Provide dynamic dashboards of equipment performance (for operations).
- Eliminate (automate) systematic preventive maintenance.
On equipped functions/equipment:
Systematic preventive maintenance operations involving checking the condition of equipment (which is correct 90% of the time) are 95% eliminated with CBM.
With remote diagnostics, 90% of corrective maintenance operations carried out AFTER a breakdown have been eliminated.
Gains measured on series where the approach has been implemented:
- Up to -50% in visible breakdowns (reliability multiplied by 2).
- Up to -30% in the number of machines stopped for maintenance. 30% fewer visits to maintenance sites.
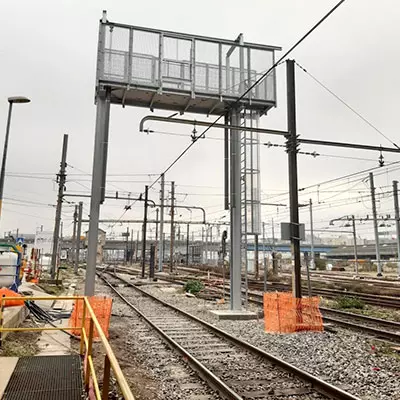
2 . Automated maintenance benches (BAM)
The BAM is a scanner that analyzes the train's vital functions.
Objectif
Take measurements and detect anomalies on train components (axles, discs, brake linings and shoes, pantographs, bogies, side panels and underbody components).
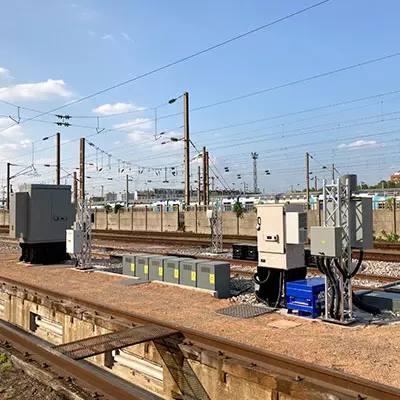
Composition
A set of 8 to 10 modules installed on a traffic lane, adapted to maintenance needs and equipped with laser sensors, high-definition cameras and calculation and analysis algorithms.
A data server.
A user interface.
Decryptage
Using an interface, operators access measurement data, automatic fault detection alerts and their location. Installed trackside, lasers and HD cameras map the components to be inspected as the train passes, from a distance of 1 meter, at 25 km/h, with an accuracy of 0.1 mm. In all, 230 wheel measurements and 420 braking system measurements are carried out in 25 seconds on a TGV. Intensified testing in 2022 has led SNCF Voyageurs to develop fault characterization methods and algorithms, new maintenance criteria specific to this revolutionary tool (one of the modules is an SNCF world first) and an associated user interface.
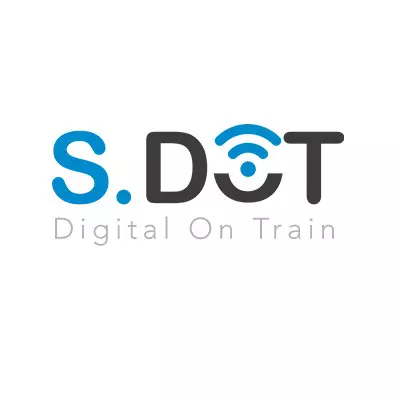
3. The communicating train
Today, running and maintaining trains is no longer enough. With the arrival of competition on French territory, but also with the firm determination of SNCF Voyageurs teams to win new European markets, equipment engineering is proposing sustainable and reliable solutions to bring more comfort and services to our customers and organizing authorities, and facilitate operation and maintenance for the operator. The aim is to design an increasingly intelligent train, capable of receiving and sending relevant information to different types of actor in real time and automatically. This is the communicating train! Both a commercial and innovative project, it is interfaced by the S.DOT (Digital Train Solution) range of services, offered à la carte.
One range, four service offerings
- Passenger Experience for all functions used by passengers (on-board passenger information system, wifi, etc.).
- Safety & Security to improve operational safety and enhance passengers' sense of security.
- Maintenance Services for communicating functions used by maintainers. S DOT facilitates the transmission of maintenance data to the ground and contributes to predictive maintenance.
- Supervision & Monitoring for functions used by the operator.
Communicating trains showcase SNCF Voyageurs' mastery of technical solutions. With S DOT, our equipment engineering department offers a global, reusable and standardized solution, applicable to the widest possible range of rolling stock. This innovative approach has been adopted by our customers.
By 2024, 360 NATs will be equipped with the Train Digital network for rear vision.
By 2032, services will be deployed on a potential 930 AGC and RER NG trainsets as part of the OPTER program.
4. Additive manufacturing
Additive manufacturing, the industrial equivalent of 3D printing, meets 2 objectives:
- Manage the supply of obsolescent parts, end-of-life, slow rotations, supply disruptions, and even reduce the costs inherent in storage and lead times.
- Design, manufacture, optimize and repair.
Decryptage
Additive manufacturing technologies combine digital design and the rapid manufacture of mechanical parts or fittings, in metal or polymer, through the successive addition of layers of material. With short lead times (from 5 to 21 days, compared with several months for conventional processes such as machining or casting), this method offers flexibility and different inventory management. At SNCF Voyageurs, 10.5% of our references are eligible for additive manufacturing.
A real feat of additive manufacturing was achieved in partnership with the École Centrale de Nantes. A large-scale pivot interface between the bogie and the body was produced and tested. This test confirms the maturity of the technology and its full potential.
Header : © SNCF
4 innovative maintenance solutions : © SNCF
Paragraph : © SNCF / SNCF / SNCF
Learn more : © ©sncf / Sébastien Godefroy / Alex Profit